Parking Lot Paving Near You
Can’t find what you are looking for?
How It Works
-
Answer a few questions about your home project.
-
Within seconds, get matched with top-rated local pros.
-
Compare quotes and choose the best pro for the job.
Parking Lot Paving In Your Area
Parking Lot Paving: What You Need to Know
Meta Description: Discover the essentials of parking lot paving, from materials to costs. Learn how to choose the right surface for your needs and ensure a durable, attractive parking area.
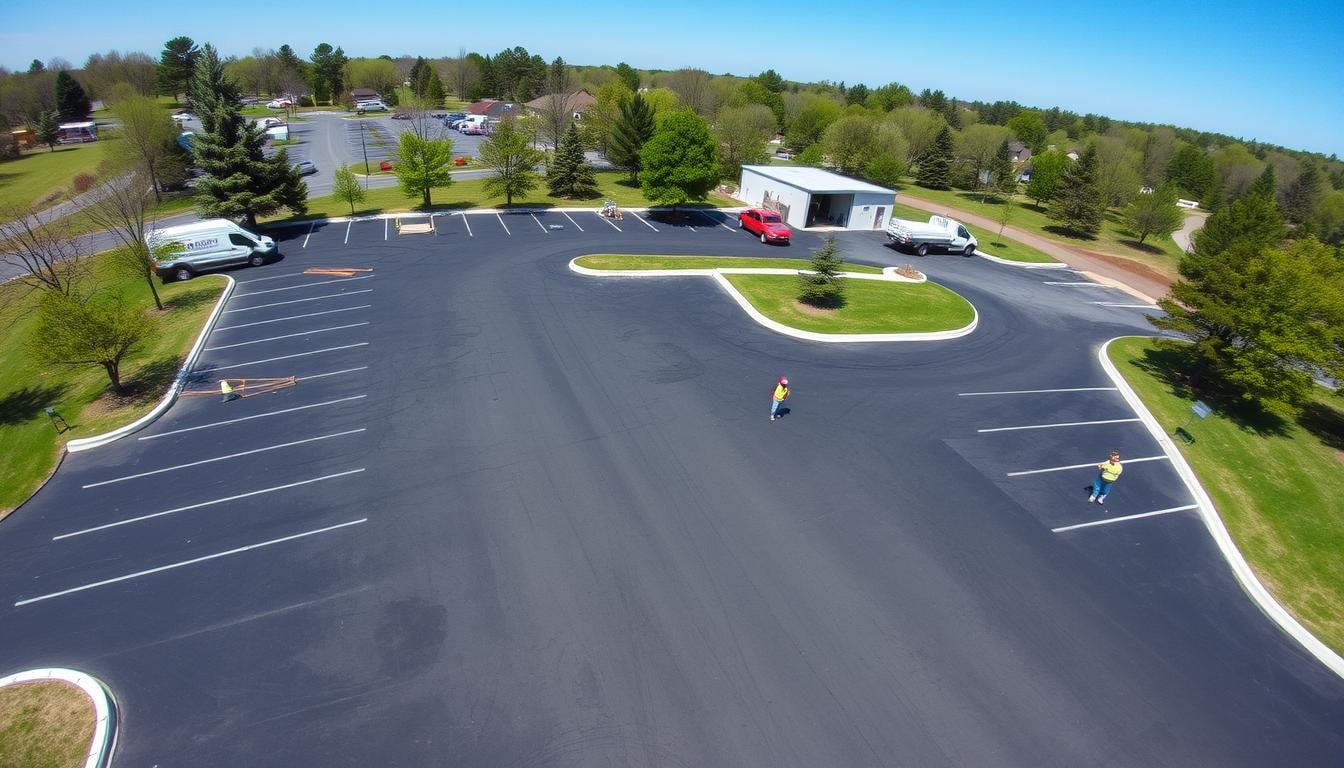
Paving your parking lot is a vital decision for business owners and property managers. It affects your property’s look, function, and long-term costs. This guide covers key aspects of parking lot paving.
We’ll explore the paving process, costs, upkeep, and environmental impact. We’ll also help you choose between asphalt and concrete for your project.
Is your current parking lot meeting your business needs? Learn how to invest in a lot that serves your property best.
Key Takeaways
- Properly constructed parking lots with good drainage systems can prevent standing water issues and damage.
- Paved parking lots with a solid gravel base can last 20-30 years with proper maintenance.
- Asphalt is a common material for parking lot construction due to its lower cost and quicker installation times.
- Parking lot paving costs can range from $2.50 to $5 per square foot, depending on various factors.
- Routine maintenance, such as pothole repair and sealcoating, is essential for extending the lifespan of a parking lot.
Introduction to Parking Lot Paving
A well-paved parking lot is crucial for businesses and property managers. It boosts property value and creates a great first impression for customers. Careful planning ensures a durable, attractive, and cost-effective solution for your property.
Importance of a Well-Paved Parking Lot
A good parking lot can greatly impact a business’s property value and customer experience. It enhances safety for both pedestrians and vehicles. A well-designed lot ensures proper drainage and accessibility.
Factors to Consider Before Paving
Business owners and property managers should think about several key factors. These include the surface material, existing lot condition, and expected traffic volume.
- Desired surface material (asphalt or concrete)
- Condition of the existing lot
- Expected traffic volume and vehicle types
- Drainage requirements
- Maintenance needs
- Environmental impact
Thoughtful planning leads to a long-lasting, functional parking lot. This enhances property value and improves the overall customer experience. A well-executed project is a smart investment for any business.
Choosing Between Asphalt and Concrete
Asphalt and concrete are the top choices for parking lot paving. Each material has its own pros and cons. Property owners should weigh these factors carefully before making a decision.
Advantages and Disadvantages of Asphalt Parking Lots
Asphalt parking lots cost less to install than concrete ones. They’re quick to set up, ready for use in just two days. However, asphalt needs more upkeep, especially in cold climates.
This material can suffer damage from harsh weather and heavy traffic. Despite these drawbacks, asphalt remains a popular choice for many property owners.
Advantages and Disadvantages of Concrete Parking Lots
Concrete parking lots are tougher and can handle heavier loads. They resist weather changes better, making them ideal for warmer climates. These lots can last over 40 years with minimal maintenance.
However, concrete costs more to install and can be harder to fix. Annual cleaning and joint sealing are usually enough to keep them in good shape.
Your choice between asphalt and concrete depends on your property’s needs. Consider your budget, local climate, and weather conditions. Also, think about durability, maintenance, and environmental impact when picking your paving material.
The Parking Lot Paving Process
Paving a parking lot involves multiple steps. It starts with site prep and ends with final striping. Careful planning ensures a durable and appealing result.
Site preparation is the first step. This may include excavation, grading, and installing a stable base. Proper compaction of the sub-base material is crucial to prevent future stability issues.
Next, the paving material is applied. For asphalt lots, old asphalt is removed to the subgrade layer. This prevents old cracks from showing through the new pavement.
Asphalt is poured and compacted using specialized equipment. This ensures even and consistent application. The equipment ranges from 8-20 feet wide.
For concrete lots, the concrete is poured and smoothed. The final step adds striping and markings. This includes parking stalls, directional arrows, and handicap spaces.
The paving process can take days to weeks. Project size and complexity affect the timeline. Working with experienced contractors ensures the job meets necessary specifications.
The construction timeline typically includes these steps:
- Site preparation, including excavation, grading, and base installation
- Asphalt application or concrete pouring, depending on the chosen material
- Striping and markings to delineate parking spaces, traffic flow, and other essential features
This parking lot paving process creates functional, attractive parking lots. It meets the needs of customers and visitors. Property owners and contractors can achieve long-lasting results.
Site Preparation and Base Installation
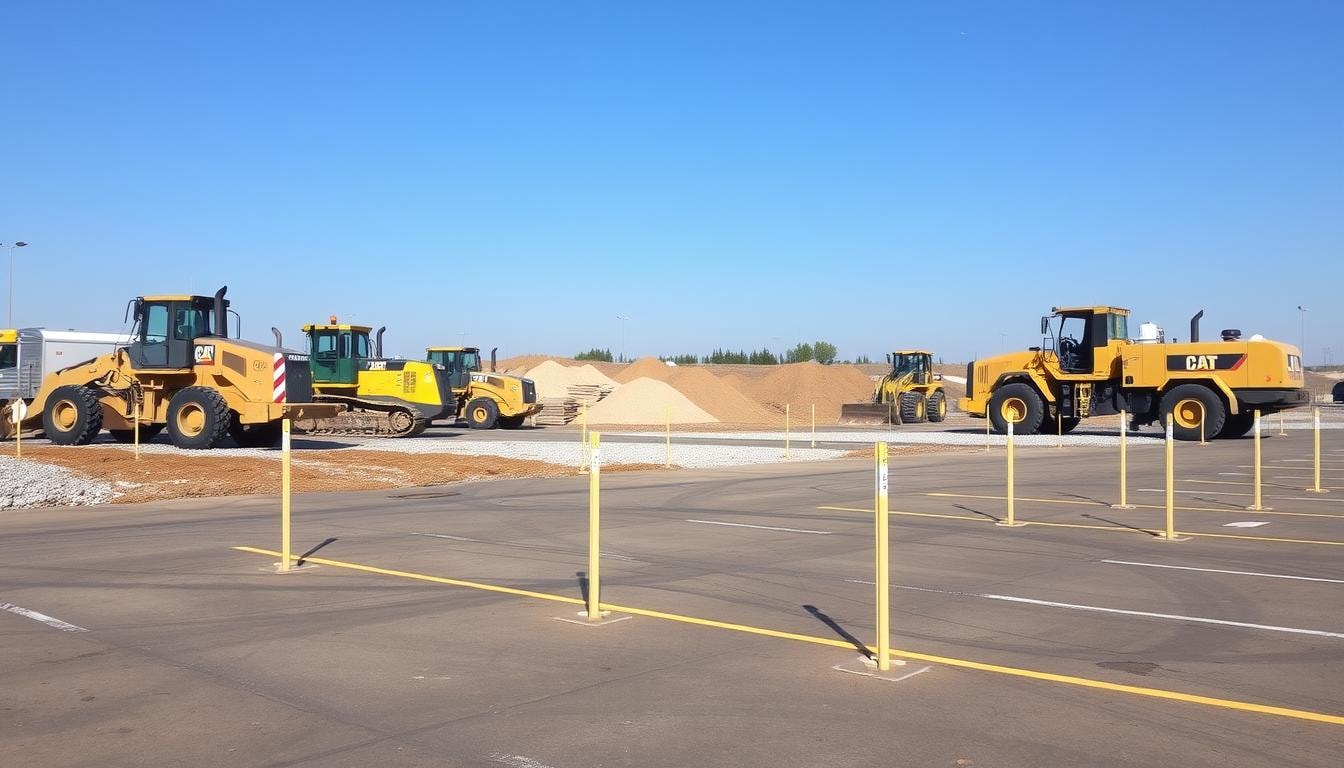
Proper site prep and base installation are vital for parking lot paving success. First, evaluate soil conditions and ensure proper grading for drainage. Create a slight slope of 1-2% to direct water runoff away from the lot.
Importance of Proper Grading and Drainage
A stable base of compacted gravel or crushed stone provides a solid foundation. The base layer’s thickness varies based on traffic volume and soil conditions. Proper compaction prevents settling and preserves pavement integrity.
Poor site prep can cause cracking, sinking, or uneven surfaces. Drainage issues may lead to water pooling, damaging the asphalt or concrete. Good preparation reduces repair costs and extends pavement life.
- Clearing the site of existing structures, vegetation, and debris
- Excavating the area to the desired depth
- Grading and leveling the site to ensure proper drainage
- Compacting the soil to create a stable foundation
- Installing the base layer of compacted gravel or crushed stone
Focus on proper site prep and base installation for durable parking lots. This approach ensures surfaces that withstand heavy traffic and environmental conditions.
Asphalt Mix Design and Application
Creating a durable parking lot requires careful asphalt mix design and application. The mix combines aggregates like crushed stone with a bituminous binder. Its composition is tailored to expected traffic volume and vehicle weights.
Heavier traffic needs a thicker asphalt layer and stronger mix. Proper application and compaction are vital. This ensures a smooth surface and prevents premature cracking or rutting.
Considerations for Traffic Loading and Vehicle Weight
The asphalt mix design must consider expected traffic loading and vehicle weights. Important factors include pavement thickness, aggregate composition, and binder type.
These elements ensure the asphalt can handle heavy equipment and commercial vehicles. Proper compaction during application is crucial to prevent future issues.
Parking Lot Striping and Markings
After paving cures, striping and markings are crucial for parking lots. These elements guide traffic, mark spaces, and ensure safety. They’re vital for directing cars and protecting pedestrians.
Parking lot striping includes lines for spaces, arrows, and crosswalks. Handicap spots must be clearly marked to meet ADA rules. The paint should be visible, tough, and weather-resistant.
Good striping makes parking lots work better and look nicer. It helps drivers and walkers move safely. Striping costs about $0.04 per square foot. Special marks like arrows cost extra.
Different paints are used: oil-based, water-based, and thermoplastic. Painting time depends on lot size and paint drying. Most paints dry in an hour and cure in four.
State rules require businesses to follow parking guidelines. This ensures access for all and avoids fines. Following rules keeps parking safe and open to everyone.
Pro stripers use laser guides and special tools. These help make precise, professional-looking markings. Weather can affect how long paint takes to dry.
- Importance of clear parking lot markings for pedestrian safety and ADA compliance
- Types of parking lot striping including lines, arrows, and crosswalks
- Factors to consider when selecting paint types and application
- Regulations and guidelines for parking lot striping and traffic flow
- Use of advanced technologies by professional pavement stripers for precise and durable parking lot markings
Parking Lot Paving Costs
Paving a parking lot’s cost varies based on size, material, and site conditions. Asphalt costs $2.50 to $4.00 per square foot. Concrete ranges from $6.00 to $8.00 per square foot.
These prices cover materials, labor, and equipment. Long-term maintenance and repair costs should be considered too. Asphalt may need more frequent upkeep than concrete.
The choice between asphalt and concrete depends on budget and specific needs. Consider expected lifespan and maintenance requirements when deciding.
Cost Breakdown for Asphalt vs. Concrete
Asphalt costs include site prep, base installation, materials, paving, and additional features. Concrete parking lots cost $10 to $20 per square foot for materials and labor.
Each parking space may cost $405 to $1,134. Repaving an asphalt lot every 15-20 years costs $1.50 to $3.50 per square foot.
Maintenance and Longevity
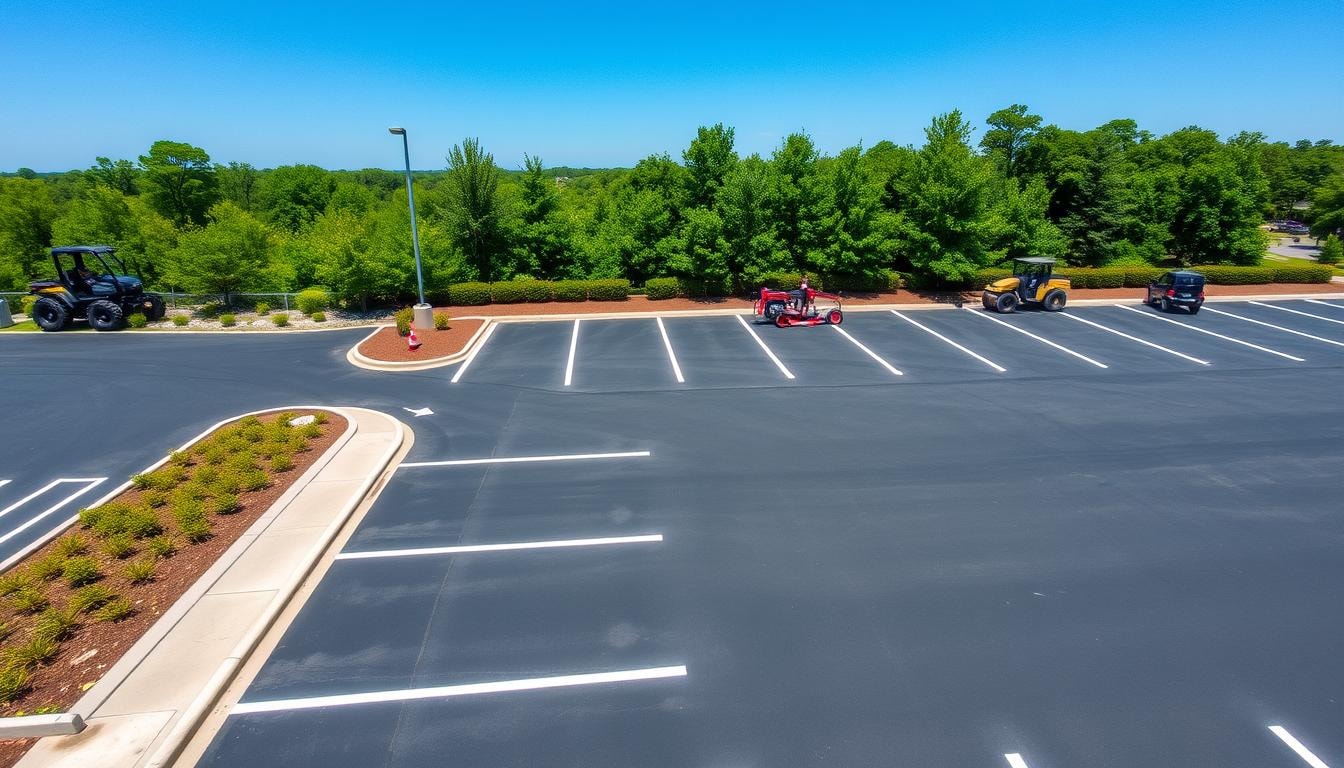
Regular upkeep is crucial for your parking lot’s durability and appearance. It extends the lifespan of your investment and helps avoid costly repaving projects.
Routine Maintenance Practices
Asphalt parking lots need sealcoating every two to three years. Prompt crack filling, pothole repair, and regular sweeping are also important. These steps can double your asphalt surface’s lifespan from 5 to 10 years or more.
Concrete parking lots require crack repairs and addressing spalling or chipping. Maintaining the drainage system is also essential. These tasks can extend your concrete parking lot’s life to 50 years.
Extending the Lifespan of Your Parking Lot
With proper care, asphalt parking lots can last 20 to 30 years. Concrete parking lots may endure up to 50 years. Traffic patterns, weather, and initial construction quality affect longevity.
Regular parking lot maintenance includes sealcoating, crack filling, and pothole repair. Sweeping and drainage maintenance are also important. These tasks maximize lifespan and durability, leading to significant cost savings over time.
Environmental Impact of Parking Lot Paving
Parking lots are essential for many properties, but their construction affects the environment. Traditional paving materials contribute to high greenhouse gas emissions. These surfaces can also disrupt natural stormwater drainage, causing increased runoff and water pollution.
Some property owners are choosing sustainable solutions like permeable pavers. These allow water to infiltrate the ground naturally. By selecting materials that minimize carbon footprint, owners can reduce their project’s environmental impact.
USDA Forest Service research shows shaded parking lots can lower surface temperatures significantly. Trees in parking lots offer many benefits. These include better stormwater management and reduced greenhouse gas emissions.
As parking lot demand grows, sustainability must be a priority. Permeable pavers, strategic tree placement, and green infrastructure can help. These methods reduce environmental impact and create a more sustainable built environment.
- Permeable pavers allow water to infiltrate the ground naturally, reducing stormwater runoff and potential water pollution.
- Strategically placed trees in parking lots can help reduce the urban heat island effect, improve air quality, and enhance the overall aesthetic appeal of the environment.
- Sustainable materials and construction techniques, such as recycled asphalt or low-carbon concrete, can help minimize the carbon footprint of parking lot paving projects.
Parking Lot Lighting and Safety
Effective parking lot lighting is crucial for safety and security. It improves visibility, deters crime, and guides traffic flow. LED lights are now the top choice for parking lots.
LEDs offer energy efficiency, long life, and bright, directional lighting. When planning lighting, consider lot size, layout, and local regulations. Good lighting enhances user experience and reduces accident risks.
The National Safety Council reports 50,000+ crashes in parking areas yearly. These result in 500 deaths and over 60,000 injuries. Proper lighting is key to preventing crimes and accidents.
LED lights last longer and use less energy. A color temperature of 4000K-5000K improves visibility without glare. This boosts safety for both pedestrians and vehicles.
Other safety measures are also important. Consider security patrols during night hours. Use access control like key cards for private lots.
Provide required handicap-accessible spaces. Implement smart parking systems to guide drivers. These steps create a safer parking experience.
Prioritizing lighting and safety measures creates a secure environment. This enhances user experience and reduces risks. Parking lot owners can make a big difference with these steps.
Hiring a Professional Parking Lot Paving Contractor
Partnering with a reputable contractor is vital for a successful parking lot paving project. These experts have the skills to deliver top-notch work and great service.
When choosing professional paving contractors, keep these factors in mind:
- Qualifications and Experience: Seek contractors with a solid history of successful projects. Check their licenses, insurance, and industry experience.
- References and Past Projects: Request client references and review their completed work. This shows their project management skills and customer satisfaction levels.
- Attention to Detail: A skilled paving contractor will understand your needs and create a detailed plan for your project.
Working with an experienced professional paving contractor ensures your parking lot is built to last. This investment can boost your property’s appeal and attract more customers.
Don’t risk your parking lot’s quality with DIY or inexperienced help. Choose a professional paving contractor for a durable result that serves you well.
FindPros: The Easy Way to Find Reliable Paving Contractors
As a property manager or business owner, you know the importance of a well-maintained parking lot. Whether you need to pave a new lot or revamp an existing one, FindPros can connect you with the best local paving contractors for the job. Unlike traditional search methods, our platform allows you to compare quotes from multiple pros, ensuring you get the best pricing and find the right fit for your unique needs.
Simply answer a few quick questions about your asphalt pavement or concrete paving project, and we’ll match you with top-rated experts who can handle everything from site preparation to pouring asphalt layers and ensuring ADA compliance. Say goodbye to the hassle of researching paving services and hello to a streamlined, low-maintenance solution that will have your parking lot looking its best for years to come.
Conclusion
Paving a parking lot is a big investment for property owners. It’s crucial to understand key factors for a successful, long-lasting outcome. This includes choosing between asphalt and concrete, proper site preparation, and ongoing maintenance.
Careful consideration of materials, costs, safety, and environmental impact is essential. These decisions will serve property needs for years. Working with an experienced paving contractor ensures high-quality, durable, and cost-effective results.
Asphalt offers durability, while concrete provides aesthetic appeal. Efficient resurfacing can minimize downtime. A strategic approach to parking lot paving is key.
Prioritizing proper grading, maintenance planning, and regulatory compliance is crucial. This creates a safe, sustainable, and appealing parking facility. It will meet the needs of both businesses and customers.
Frequently Asked Questions (Parking Lot Paving)
MOST POPULAR CITIES
Browse by State- Alameda
- Costa Mesa
- Laguna Beach
- Orange
- Alhambra
- Culver City
- Lancaster
- Oroville
- Anaheim
- Daly City
- Livermore
- Oxnard
- Antioch
- Davis
- Lodi
- Pacific Grove
- Arcadia
- Downey
- Lompoc
- Palm Springs
- Bakersfield
- El Centro
- Long Beach
- Palmdale
- Barstow
- El Cerrito
- Los Angeles
- Palo Alto
- Belmont
- El Monte
- Malibu
- Pasadena
- Berkeley
- Escondido
- Martinez
- Petaluma
- Beverly Hills
- Eureka
- Marysville
- Pomona
- Brea
- Fairfield
- Menlo Park
- Port Hueneme
- Buena Park
- Fontana
- Merced
- Rancho Cucamonga
- Burbank
- Fremont
- Modesto
- Red Bluff
- Calexico
- Fresno
- Monterey
- Redding
- Calistoga
- Fullerton
- Mountain View
- Redlands
- Carlsbad
- Garden Grove
- Napa
- Redondo Beach
- Carmel
- Glendale
- Needles
- Redwood City
- Chico
- Hayward
- Newport Beach
- Richmond
- Chula Vista
- Hollywood
- Norwalk
- Riverside
- Claremont
- Huntington Beach
- Novato
- Roseville
- Compton
- Indio
- Oakland
- Sacramento
- Concord
- Inglewood
- Oceanside
- Salinas
- Corona
- Irvine
- Ojai
- San Bernardino
- Coronado
- La Habra
- Ontario
- San Clemente